A Complete Guide to Machine Safety
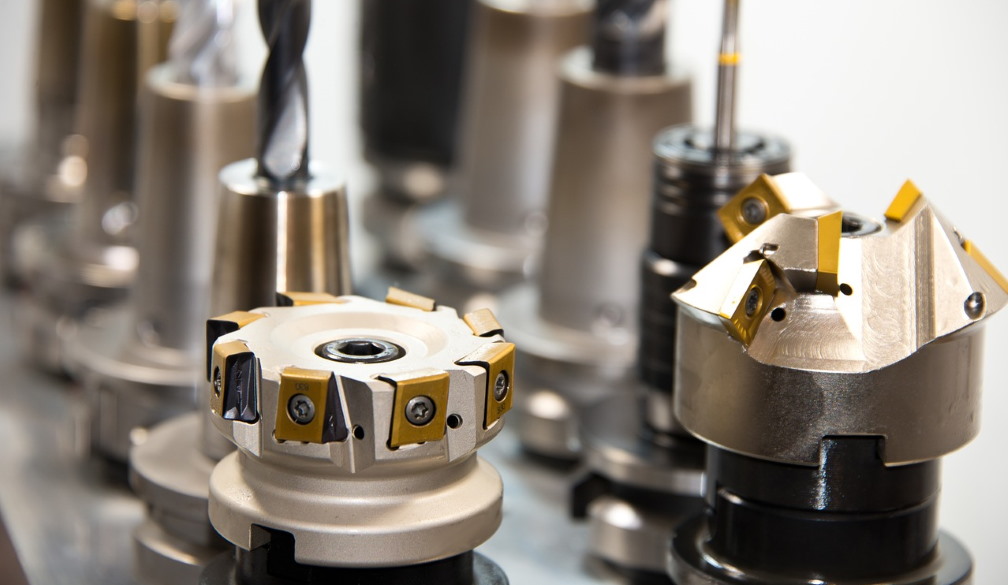
Machine safety is the first requirement in the factories and industries as well as the machine itself. It ensures the security of both the machine and its handler. The use of tools like rebar benders comes into play for machine safety. This guide will help you to realize why safety measures are important and how to ensure these.
What is machine safety?
Machines and equipment from places like Platforms and Ladders increase productivity, still, they can cause mild and serious injuries such as crushed or broken fingers and toes, mutilations, skin burns, blindness, traumas, or even deaths.
Injuries can be caused by machines’ parts, functions, or processes. Machine safety is the way of hazardous parts to be safeguarded, removed, or controlled. As we progress with technology, we see enhanced machine safety.
Why is machine safety important?
Machine safety is a must for various aspects. Some of the major requirements are like:
- * Continue the production
- * Keeping the productivity along the whole time of production hours
- * Avoid any human injuries
- * Keeping safe human lives
Types of machine injuries
Machinery can cause harmful injuries in many ways. Few types are like:
- * Sharp edges: Cut or puncture skins, fingers, nails, etc.
- * Rough surfaces: Causes scratched skin.
- * Moving parts: People or their hands or legs may get trapped between moving parts like belts, rollers, needles resulting in crushed skulls, bones.
- * Hot surfaces: Often results in skin burns.
- * Leaked oils or hot steams: Burn skins, affect eyesight, and even cause blindness.
- * Bad UX design: This leads to improperly handling or operating, which often damages the machine itself.
- * Electric sparks: High voltage machines burn, unconsciousness, and even cause blindness.
Which tools are the best for machine safety?
Now it comes to the point of what to be used for ensuring machine safeties, here we can look at some of the small and big stuff:
- Tower light: The tower lights are visible from long distances and from all angles, bringing real-time indications of hazardous motions or unusual situations.
- Safety interlock switches: When guards like a gate, door or panel get opened or removed automatically or by any individuals, the switch sends a signal to the control system to freeze the hazardous operations.
- Indicator lights: LED Indicators to provide high-visibility real-time indication of equipment and safety status.
- Safety scanner: This scanner protects both handlers and machines within a user-designated area. It’s ideal for safeguarding complex and uneven areas and wandering assets.
- Safety controller: This device monitors multiple safety and non-safety input devices, ensuring safe stop and start functions for machines.
- Enabling devices: When the handler either squeezes or releases the handle grip switch, this device leads to a safe operation, it also allows the machine in manual operating mode.
- Safety light curtains: It protects people by creating a sensing screen, which guards entry points and perimeters of the machine. When anybody interrupts, it will trigger a cutoff to the hazardous motion.
- Emergency stop: Emergency stop allows you to immediately stop a device by simply pressing a button or pulling a rope, which removes power from hazardous motions.
- Two-hand control devices: This device keeps the operator at a secured distance from risky or unsafe motions. If operators’ one or both hands are displaced from the device, the hazardous motions stop working.
- Machine guards or fences: Industrial safety fencing or guarding systems or perimeter fencing, is designed to keep a safe distance between the operators and machines.
- PPE: Including safety helmets, gloves, eye protectors, high-visibility clothing, footwear, and safety armor, PPE protects against health or safety risks in hazardous situations.
Which are the main machine safety regulations
Below are few safety guidelines followed over the world:
- ANSI / NFPA / RIA / ASME / MIL Safety Standards
- ANSI B11 Machine Safety Standards and Technical Reports
- IEC / ISO International Safety Standards
- Applicable OSHA Machine Safety Standards
Some of Machine Safety Guidelines
- Reading manuals: Always reading the machine operating manuals thoroughly, even for a basic machine. Operations and handlings may vary between various producers
- Checklist: Must having a checklist, as the aircrews check before every flight
- Regular Checking: Maintaining the regular checking and doing the necessary maintenances
- PPE: Wearing personal protective equipment is a must obligation,
- Training: Training the operators before handling, get them, familiars, with various parts and operations
- No Jewelry: Removing any kind of jewelry like rings, earrings
- Neat & Clean: Keeping the floors and surroundings always neat, clean
- No leaks: Ensuring no leaks of steams or waters
- Safe distance: Maintaining safe distance as per manuals
- Emergency buttons: Checking the emergency stop button is working
- Keeping record: Maintaining the written record of machines repairing, modifications
- Dry floor: Slippery floor is a major cause of accidents, ensuring dry floors and walls are a must need.
- Expired machines: Expired machines must be sent to retirement.
Importance of Human behavior in machine safety
Major accidents are caused because of the mental health of the operators. Some basic rules can be followed to ensure operators fully present in their tasks
- No distraction: Any kind of distraction has to be discouraged; operators must be in full attention
- No overwork: Discouraging operators from doing the double shifts either forced by management or from their choices
- Happy stuff: Operators sometimes are not happy with remuneration and have a tendency to do harm to the machines
- Following rules: People have a tendency to bypass the manual prepared by the technicians in the moment laps, their mental health should be checked.