Avoiding Common Mistakes When Installing Warehouse Pallet Racking
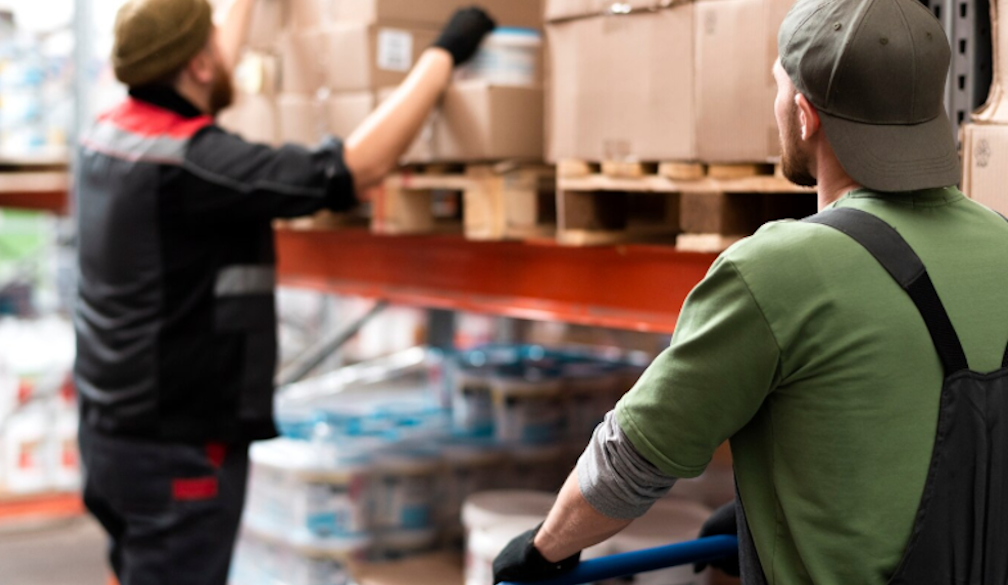
Let’s face it: warehouse pallet racking is the unsung hero of any efficient storage system. It’s the backbone of your operations, the silent organiser that maintains your stock reachable, your workflow clean, and your warehouse jogging like a nicely-oiled device. But here’s the seize—getting it right isn’t as simple as bolting some beams together and calling it an afternoon.
Installing warehouse pallet racking is like assembling flat-percent furniture but on a far larger, more crucial scale. You could handle costly delays, safety risks, or even a machine collapse with one incorrect pass.
In this blog, we’ll walk you through the most common mistakes businesses make while putting in pallet racking and proportion practical suggestions to help you avoid them. Whether you’re putting in a new warehouse or revamping a current one, this manual will make sure your racking machine is sturdy, safe, and prepared to handle something your business throws at it.
1. Failing to Plan for Future Growth
The major error organisations commit involves considering only present-day storage requirements. The warehouse environment continuously evolves because product quantities, dimensions, and operational demands experience regular alterations.
How to Avoid This Mistake:
- Your racking system needs to account for upcoming business expansion possibilities.
- Select storage solutions which provide expandable capabilities for possible growth modifications.
- A racking specialist should help create a layout design that lets your business expand without affecting daily operations.
Your cost savings from good rack planning will occur by preventing future expensive retrofits.
2. Choosing the Wrong Type of Racking
The market features multiple warehouse pallet racking system designs that differ in their characteristics. Your warehouse racking decision must match product requirements, available space, and establishment selection methods. Installing an inappropriate system results in ineffective operations, space loss, and potential damage to your stored goods.
Common Types of Racking and Their Uses:
- Selective Racking: Ideal for warehouses with a high stock turnover and direct access to each pallet.
- Drive-In/ Drive-Through Racking: Users can efficiently store bulk items using Drive-In/Drive-Through Racking though the system restricts direct access to products.
- Cantilever Racks: They are the best solution for storing long bulk objects such as steel, pipes, and timber.
- Push-back Racking: The push-back system delivers dense storage options and complete accessibility to stored products.
How to Avoid This Mistake:
- Conduct an inventory process assessment and analysis before picking a racking system.
- Proper analysis should incorporate weight measurements, size assessments, and turnover calculation frequencies.
- Consulting with an expert helps you select the right racking type which suits your business operations.
3. Ignoring Load Capacity and Weight Distribution
Overfilling product racks results in a catastrophic event. Failure to design racks for product weight creates dangerous scenarios, threatening staff safety and damaging stock.
How to Avoid This Mistake:
- Your racking system requires constantly checking its maximum load capacity and strict adherence to approved figures.
- The distribution of merchandise weight across shelves should maintain even distribution to avoid point-stress areas.
- The establishment should use visible warning signs to establish weight limits and staff training on these restrictions.
- Modular Benefits cover conducting scheduled system checks for signs of overweight conditions and structural breakdowns.
The first principle of warehouse safety involves weighing everything correctly because shortcuts cannot be acceptable.
4. Poor Floor Space Utilisation
Warehouses possess valuable space that becomes wasted due to suboptimal rack system planning. A system designed without attention to detail produces bottlenecks, decreases storage space, and affects pallet accessibility.
How to Avoid This Mistake:
- You must develop appropriate aisles for your forklifts and pallet jacks to achieve optimal material handling performance.
- Vertically maximising space allows you to store more while keeping your total floor space unchanged.
- Implementing mobile rack systems represents an excellent approach to achieving maximum storage density.
A well-designed warehouse allows businesses to operate smoothly while properly using every potential space area.
8. Overlooking Compliance with Warehouse Regulations
All warehouses must meet their share of safety standards and industry-established regulations. Failure to comply with required standards will trigger monetary fines and possible legal troubles and force operational closure.
How to Avoid This Mistake:
- Before building warehouse pallet racks, learn about all workplace safety requirements that apply locally to pallet racking installations.
- Verify that your storage structure upholds peak weight capacity limits and all necessary fire protection standards.
- Documentation on inspections, maintenance, and weight capacity should be readily available.
Meeting all compliance standards helps protect your workforce while also preventing costly penalties.
Final Thoughts: Setting Up for Success
The installation process for warehouse pallet racking appears simple, yet people need to avoid specific mistakes. When implemented correctly, a secure and efficient storage system will ensure optimal performance. Your warehouse will reach optimal performance by implementing appropriate planning, expert installation, and scheduled maintenance activities.
Setting up a new racking system or upgrading an existing one requires proper planning to achieve successful execution on the first attempt. A warehouse designed well extends benefits beyond pallet storage because it optimises the entire operational efficiency.
Organisations are considering adding warehouse pallet racking systems. Contact an expert for guidance on establishing a warehouse system that meets current safety regulations and performance standards, as well as potential future business requirements.