Ewp Inspections: Your Key To Safety
- Written by News Company
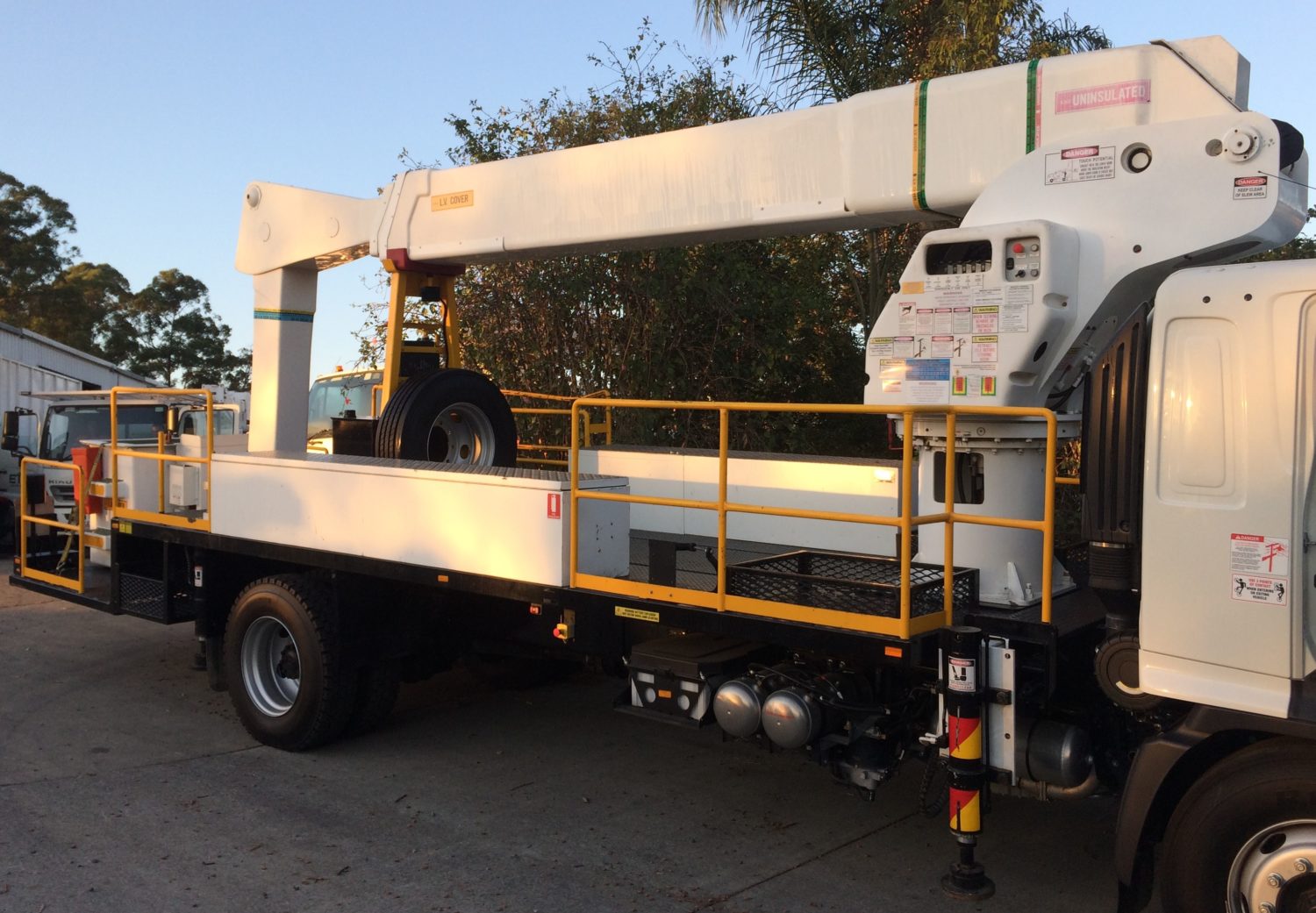
EWP stands for Elevating Work Platforms or Mobile Elevating Work Platforms. The use of EWP is a major factor in the reduction of fall mishaps / accidents at any workplace. And the use of EWP is regarded as the safest solution to enable a given temporary work at height. Its use is never risk free. There are a number of dangers associated with the use of EWP and need regular checks and inspections. If you are hiring an EWP make sure to choose the right inspection services. For EWP Inspections, EWP Inspection services offer a complete safety programme that covers all the aspects such as types of EWPs, pre-operational checks, general guidelines and all other dangers/ hazards. These include objects falling from height, collapse, crushing, trapping, tripping and control measures.
Why are EWP Inspections Important ?
Maintenance of EWP and regular inspection is important to ensure the operator’s safety. As per Australian Standard AS 2250 .10-2006 all EWPs including boom lifts, scissors lifts and telehandlers must undergo regular inspections every ten years from the date of their manufacture.
The inspection must be carried out by a trained and qualified technician who follows a strict inspection checklist keeping the components in mind and also to ensure that the unit is operating at optimal levels, and needs for an immediate replacement of components that shows signs of corrosion, fatigue or wear.
There are four major types of inspections to be undertaken regularly to ensure that the EWPs are safe and functioning properly.
- Pre-operational Inspections:- As per the Australian Standard, this inspection must be carried out by some qualified operator before commencing every work shift. This includes a physical inspection for broken tools and equipment, fatigue, corrosion and wear of major components. This also includes testing of interlocks and emergency lowering systems.
- Routine Inspection/testing:- This inspection must be completed by a trained and qualified inspector within a time frame of three months. The inspector has to verify that the units’ logbooks and manuals of the operator are up to date. Safety devices and control functions including based basket controls are tested. For breaks, wear, fatigue and corrosion, all hydraulic hoses and connections, chains and cable systems are inspected . Fluid level and filter are checked to ensure that all moving parts are lubricated. A written report is provided for any point of action after the inspection.
- Periodic Check:- A periodic inspection must be done by a qualified person based on the EWPs working environment, workload and usage frequency, not exceeding twelve months interval. In-depth inspection including dismantle of parts to ensure that they are still fit for the work and needs no replacement is necessary. A flexible suspension and a stability test in every fifth year of operation and every two years thereafter is a must with EWP .A unit cannot return to work until all damaged parts have been replaced, all safety measures are taken and all problems have been rectified by a qualified inspector.
- Major Inspection:- If a unit has not been subjected to routine or periodic inspection and has been working for more than ten years, EWPs have been imported without having any previous maintenance record, then such inspections are to be carried out. This includes a full strip down of the unit and its components, all paint, grease and corrosion from the components to be removed by a complete physical inspection including structural welding.
Conclusion:- The EWP Inspecting Services provide all these types of inspective services to ensure you an effective and better functioning EWP for your project and also provide tips and advice with safety solutions. Their aim is to show the necessity of operating EWPs safely and by doing that; they increase awareness standards for workers, being active and responsible in daily safety plans of action.