Investment Casting Process-Advantages of Investment Casting Applications
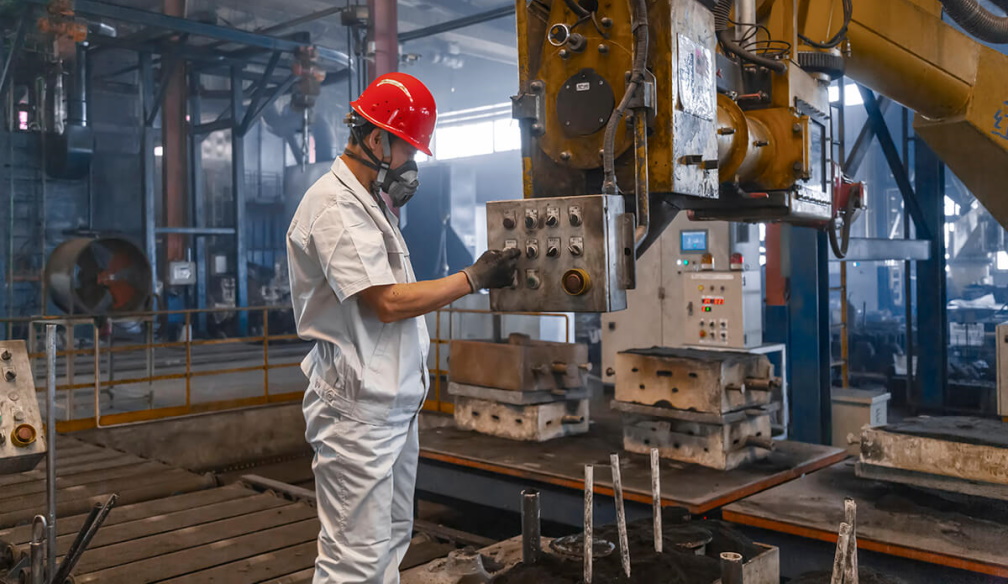
What is the investment casting process?
Investment casting process is a metal casting technique in which the molds are made from finely ground materials such as plaster, clay, graphite, or ceramics. The mold is then heated in a kiln to become hard and durable. Alloys of various compositions can then be poured into the mold to produce a variety of shapes and sizes.
Investment casting is an intricate manufacturing process that has many benefits and advantages over other manufacturing processes. Investment Casting Applications is a metal casting technique in which the molds are made from finely ground materials such as plaster, clay, graphite, or ceramics. The mold is then heated in a kiln to become hard and durable. Alloys of various compositions can then be poured into the mold to produce a variety of shapes and sizes.
Investment casting process
Investment casting is a very old technique in which incredibly detailed patterns are created for the mold in a process called lost-wax casting, in which a model of the desired part is formed in wax and then enclosed within a clay shell that will ultimately become the investment mold. When heated above 1200 degrees Celsius, the wax melts and runs out of the bottom of the mold. The now-empty space is filled with molten metal and solidifies to form a very fine replica of the lost wax model.
Investment casting involves making a ceramic shell, often using materials such as plaster (Gypsum), and then pouring molten metal into the shell. The principle behind this is that metal has a high melting point, but at the elevated temperatures needed to melt it (about 1,600 degrees Fahrenheit), the mold material will not survive long enough for it to solidify. This method allows you to make larger and more complicated shapes than you could if you were just making one piece. The technique was originally developed in ancient Egypt about 5,000 years ago.
Investment casting manufacturers and companies:
There are many companies manufacturing investment casting across the world. The process is adopted by many industries but is more commonly used in aerospace, medical, historical restoration, craft making etc. Some of the popular manufacturers of Investment Casting Process include - dawangcasting.com - Oakley Industries , JMT Fluid Components Pvt Ltd, Precision Investment Casting, Inc., HMC Fluid Power Pte Ltd etc.
Advantages Of Investment Casting Applications:
The investment casting process has some definite advantages over other manufacturing processes. It can be used to produce intricately detailed parts with varying cross sections and long undercuts. The ability to use natural or synthetic materials as mold material provides the designer with almost unlimited design freedom. Investing in this technology will allow you to produce small to large batches of parts helping your business achieve higher production rates. In time, as the need for costs associated with the process is reduced and quality continues to improve, this technology will play a larger role in fluid management. Let's see 10 common advantages:
1. Ability to make intricate designs.
2. Low tooling cost compared to other casting processes. Lowest cost form of metal casting process in terms of initial investment needed for a factory.
3. Ability to produce large, complex parts with internal features and intricate undercuts as well as thin walls.
4. Can be used for prototyping to validate process before expensive tooling is created
5. Natural or synthetic materials can be used as a mold material depending on requirements of the product being casted from it.
6. Good surface finish.
7. Capability to make many castings quickly without the need for detailed finishing post-casting.
8. Can be used with a variety of metals and alloys, although it is typically only used with precious metals like gold, silver, platinum etc. Because it can't be used with ferrous materials like steel, the investment casting process is typically used for smaller components or parts.
9. Ability to make components with tight tolerances and fine details. Investment casting can produce parts with tolerances as good as 0.0002 inch (0.005 mm) per inch of part cross-section diameter variation, whereas an extruded part is typically +/-0.0003 in (0.010 mm).
10. No parting lines, mold flow lines or sink marks since the mold is broken away after casting process hence no cleaning up is required.
Investment casting applications:
Investment castings are used in a wide range of industries. Most often, they are used to make metal parts that require high precision and good surface finish. Some of the most common applications where investment casting is used include -
1. Medical Sectors: These castings are mainly required by the dental industry for making artificial teeth, bridges, inlays and orthodontic appliances. Prosthetic appliances like artificial hip joints are also made by the investment casting process.
2. Automotive Sector: Investment castings are used to make components in automobiles like gear shift levers, brake pedals etc. These parts are required to be manufactured in high volumes hence they require a low-cost casting process that can produce them quickly.
3. Historical Restoration: In historical restoration, full sized castings are often created from smaller original pieces to restore the looks of antique furniture and artwork. This process is used due to its high level of precision and ability to reproduce fine details with ease. Other decorative ornaments like wall plaques, door hinges etc. can also be made using the investment casting process.
4. Industrial Sectors: There are a wide range of industrial applications where investment casting is used to produce a variety of components and parts. These include pump impellers, rollers, hydraulic jacks, seals, hydraulic valves etc. The automotive, food and beverage, chemical and machinery industries also use investment castings.
5. Architectural Applications: In architectural applications, the investment casting process is used to produce decorative items that are often made from metal or alloy materials. These include balusters for staircases, rainwater drainage system components like down-pipes and so on.
Investment molding process:
The investment casting process follows the steps listed below.
1. Pattern Making - The first step in investment casting is to create a pattern of the part that is to be casted. The type of material used for this purpose depends on the final use of the component, typically steel or aluminum are used. However, if nickel alloys are to be used for casting, they need to be wax coated as aluminum would melt in the nickel-alloy environment.
2. Wax Injection or Spruing - Since investment castings are done by a process where a mold is created around a pattern, the pattern has to have an opening that allows molten metal into the mold cavities to solidify around it. This metal is poured into the mold cavity from a flask made using wax. Wax sprues are also used to allow air and other gases to escape from the mold as the molten metal fills up the cavities.
3. Investment Cast Stainless Steel - The investment cast stainless steel process involves making a pattern out of any suitable material, typically wax or plastic. It is then coated with an anti-wetting agent and sprayed with a parting agent to prevent the metal from sticking to it during the investment casting process. The pattern is then placed in a flask along with other materials like ceramic and investments. A flexible rubber ring made out of silicone is used to create a gas tight seal between the flask and the mold. This ring is applied by hand using a soft brush. Another silicone rubber ring is used to create a tight seal around the sprue hole so that molten metal does not leak through it during casting.
4. Ceramic Molding - In this step, investment powder mixed with water is poured over the wax pattern. Ceramic is added to this mixture at this point in order to strengthen the mold. This mixture is then vibrated for about 3 minutes to ensure that the powder reaches all areas of the flask, creating a consistent thickness. The mix is allowed to dry completely before it is placed inside an oven for firing at over 1,100 degrees Fahrenheit. Once the ceramic has been fired, it forms a hard and porous shell.
Conclusion:
As you can see, the process of creating an investment casting is relatively simple and inexpensive. The use of a wax pattern ensures that a single mold can be used for multiple castings without any significant wear and tear. This makes it a good option for mass production as well as creating one off components. Since these are precision tools, even small changes in a component's design can have a major impact on its functioning. As a result, investment cast components are popularly used in industries that need high quality and accurate tooling such as the aerospace industry. Visit google books or engineering world to read more about the topic.