Cool it: Australia's biggest cold trucking firm has collapsed, but reports of a supermarket supply disaster are overheated
- Written by Flavio Macau, Associate Dean - School of Business and Law, Edith Cowan University
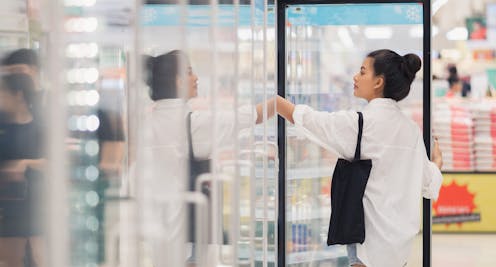
If there’s any lesson from the past three years of supermarket shortages, it’s that it pays to stock up on a few favourite items at all times (if you’ve got room in your pantry or freezer) and to be flexible in your choices of products and brands.
And don’t panic. That doesn’t help anyone.
I’ve made these points before – from the demand-driven stockpiling of toilet paper and pasta during COVID lockdowns, to the supply-driven shortages of meat, lettuce, eggs and potato chips since.
But they are worth repeating, as Australia faces another potential post-COVID supermarket shortage – this time of any groceries that require refrigerated transport (frozen food, meat, dairy and fresh fruit and vegetables) following the collapse of Australia’s largest cold-chain refrigeration transport company.
Scott’s Refrigerated Logistics – with more than 1,500 employees, 500 trucks, 1,000 trailers and warehouses in Sydney, Melbourne, Brisbane, Adelaide and Perth – was placed into administration on February 27.
Administrator KordaMentha has been unable to find anyone to buy the stricken business from Anchorage Capital Partners, a private-equity company that bought Scott’s in 2020 for A$75 million.
Without a buyer, the company will be liquidated, with its assets sold off piecemeal. KordaMentha has warned of a “genuine risk of an uncontrolled wind down”, leading to supermarket supply shortages.
This will likely mean sporadic shortages and restocking delays. But sensationalist headlines that a “supermarket disaster looms” are overblown. As long as we don’t make things worse, shortages should be short-lived – an inconvenience, but not a disaster.
Why did Scott’s Refrigerated Logistics fail?
Why has Scott’s failed, despite being Australia’s biggest cold transport trucking company? Part of the reason, at least, was probably due to being “Australia’s only truly dedicated national temperature-controlled supply chain network”.
The past few years have been difficult for trucking companies – and even more so for cold-transport trucking.
Moving goods around the world from one port to another is relatively simple. The cost of transporting an item thousands of kilometres across oceans typically adds just a few cents per unit to costs. It’s when those goods get loaded onto trucks – first to be transported from the dock to a warehouse, then to a distribution centre or store, then to the end consumer’s home – that the costs mount.
There is traffic and limits to operating hours. There are different trucks instead of standardised containers. Routes change all the time, as orders are updated daily. So-called “last-mile delivery”, from the final distribution hub to the home, is the most complicated and expensive leg, generally accounting for at least half of logistics costs.
These costs are compounded when items need to be kept cold or frozen. Refrigeration equipment is expensive to buy and maintain. Temperature controls must work seamlessly. If the refrigeration breaks down, the cargo must be quickly transferred to another vehicle.
Refrigerated warehouses and vehicles use more energy. Warehouses are coping with more heat as average temperatures rise with climate change. Vehicles must run their engines to keep their cargo cold. So increases in both fuel and electricity prices over the past year will have eroded the bottom line.
Along with these issues are the challenges facing all transport companies, such as finding drivers. There is a global shortage of truck drivers, intensified by the pandemic, which has forced employers to offer higher wages to recruit workers.
Then there is the highly concentrated nature of Australia’s grocery retail sector, with Coles and Woolworths controlling about 65% of the market (and Aldi another 10%). This puts any company in the food supply chain at a disadvantage when it comes to negotiating contracts.
Assurances from Coles and Aldi in recent days that they have contingency plans to replace the services provided by Scott’s is indicative of this power imbalance.
Read more: Floods, pandemics, wars and market forces: what's driving up the price of milk
What this means for you
So what does the risk of an “uncontrolled wind down” of Scott’s businesses mean for shoppers?
You may see gaps in the fresh food, dairy, meat and frozen food aisles similar to those in early 2022, then driven by COVID-related absenteeism among transport, distribution and shop workers. These shortages should be short-lived, as other businesses pick up the slack and supply is mended.
Read more: Supermarket shortages are different this time: how to respond and avoid panic
Thankfully, the industry has learned a few lessons from the past. Supply chain orthodoxy has moved a bit more from just-in-time to just-in-case.
Hopefully, also, most customers have learned from the past, and won’t be shocked by empty shelves. Panicky stockpiling behaviour will only makes shortages worse. Many of us (who can afford it) now also keep stocks at home in anticipation of rainy days.
Read more: 'Panic-buying' is the new normal: how supply chains have adapted
In the longer term, though, you should expect to pay higher grocery prices.
Contingency plans as those put in place by Coles and Aldi are costly, and the sustainability of the food distribution systems would indicate that supermarkets will need to pay more for refrigerated transport next time contracts are negotiated. These extra costs will most likely be transferred to you, the customer.
We have not yet turned the corner around supply chain issues. This is unlikely to be the last struggle that affects supplies. Occasional empty shelves in your local supermarket are the “new normal”, at least for now.
But, all in all, we are a better position to cope with these shocks than three years ago. So don’t panic.
Authors: Flavio Macau, Associate Dean - School of Business and Law, Edith Cowan University