Insulation Solutions for Meeting Modern Industrial Standards
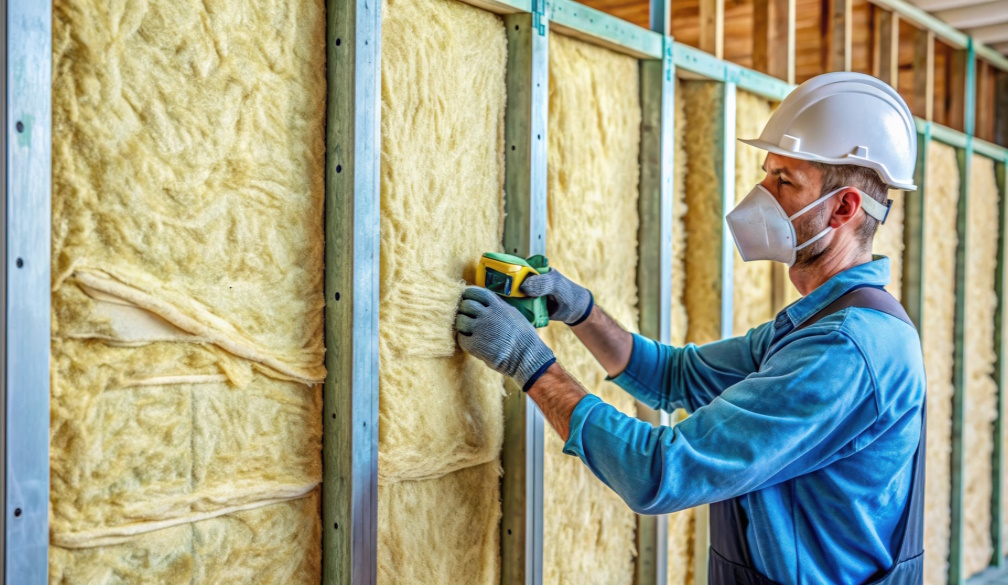
As global energy costs soar and environmental regulations tighten, industries face unprecedented pressure to optimise their operations while minimising their ecological footprint. Modern industrial insulation has emerged as a critical cornerstone in addressing these challenges, transforming from simple thermal barriers into sophisticated, multi-functional systems that define the future of industrial infrastructure.
This comprehensive exploration delves into cutting-edge solutions that are reshaping industrial standards and setting new benchmarks for performance, sustainability, and cost-effectiveness. Read on.
Advanced Fire Protection Systems
Fire protection has turned into this highly sophisticated field incorporating multiple layers of defence. New intumescent formulations by insulation manufacturers include nano-additives that enhance char strength and thermal resistance. These materials can expand up to 100 times their original thickness when exposed to heat, creating more effective thermal barriers.
Some systems now also incorporate phase-change materials that absorb heat energy while maintaining structural integrity. Advanced ceramic-based fire protection coatings can withstand temperatures up to 1800°C while remaining lightweight and easy to apply. Recent developments include smart fire protection systems that can detect and respond to heat build-up before traditional fire detection systems are triggered.
Still, we shouldn't ignore the pioneers' capabilities. One solid option when it comes to exceptional fire resistance is Rockwool insulation from FM Insulation Supplies or other reputable suppliers. Though it's been around since the early 1900s, it remains an ideal choice for ensuring safety and overall thermal efficiency in both residential and commercial buildings.
Industrial Acoustic Solutions
The evolution of industrial noise control has expanded to include innovative approaches beyond traditional methods.
New metamaterial-based acoustic panels can achieve selective frequency absorption, targeting specific noise signatures common in manufacturing environments. These materials utilise engineered resonance chambers that can be tuned to match the exact frequencies of problematic equipment. Also, advanced software modelling now allows acoustic engineers to create precise sound maps of industrial spaces, enabling targeted placement of acoustic treatments for maximum effectiveness.
Here's more: some facilities have implemented dynamic acoustic systems that adjust their properties based on real-time noise monitoring, providing optimal noise reduction during different operational phases.
Moisture Management Innovations
The field of moisture management has seen remarkable advancements in recent years. Beyond smart vapour retarders, new composite materials incorporate phase-change materials (PCMs) that provide additional thermal buffering while managing moisture. These systems can store and release latent heat energy, helping stabilise both temperature and humidity levels.
Researchers have also developed self-healing moisture barriers that can repair minor damage through advanced polymer chemistry, maintaining their effectiveness over extended periods. Some cutting-edge systems, on the one hand, incorporate graphene-based coatings that provide exceptional water resistance while improving thermal conductivity at critical junctions.
Installation and Quality Assurance Advancements
The landscape of installation methodologies has undergone quite a transformation as well. Building Information Modelling (BIM) has revolutionised pre-installation planning by enabling comprehensive 3D visualisation and clash detection. Real-time thermal mapping systems equipped with high-precision sensors can now detect variations as minute as 0.02°C during the installation process. Also, sophisticated robotics systems are increasingly being deployed for insulation installation in confined spaces, hazardous environments, and areas with limited accessibility.
Quality assurance in insulation installation has evolved to incorporate predictive analytics and artificial intelligence, forever changing how potential issues are identified and addressed. Machine learning algorithms now process vast amounts of thermal imaging data to create detailed performance models that can forecast potential failure points weeks or even months before they manifest. These systems integrate with building management platforms to provide continuous monitoring.
There are automated inspection drones too; equipped with thermal cameras, they conduct regular surveys of large-scale installations, generating detailed reports that help maintenance teams optimise their intervention strategies.
Environmental Sustainability Initiatives
The push for sustainable insulation solutions has led to innovative new materials and processes. Beyond bio-based insulation, researchers are developing carbon-negative materials that actively sequester CO2 during their production process. Some manufacturers have implemented closed-loop water systems and renewable energy sources in their production facilities, further reducing environmental impact. In addition, new recycling technologies can now separate and recover different components of composite insulation materials, enabling more effective recycling of end-of-life products.
Economic Analysis and ROI Optimisation
The economic benefits of advanced insulation systems extend beyond simple energy savings. Integration with building management systems allows for real-time optimisation of HVAC systems based on insulation performance. This means significant energy savings. Predictive maintenance algorithms? They can now factor in variables such as weather patterns, operational schedules, and equipment ageing to optimise maintenance timing and extend system life.
The development of performance-based contracting models has also emerged, where insulation providers guarantee specific energy savings levels over extended periods.
Conclusion
The solutions discussed here are stepping stones toward even more efficient and sustainable industrial operations. Success in this field now demands a holistic approach that considers thermal efficiency, acoustic performance, fire safety, and environmental impact as interconnected challenges rather than isolated concerns. For industries willing to embrace these advanced solutions, the rewards extend far beyond mere compliance – they open doors to enhanced operational efficiency, reduced environmental impact, and significant long-term cost savings.