Different Types of Commercial Waste Bins and How They Work
- Written by Daily Bulletin
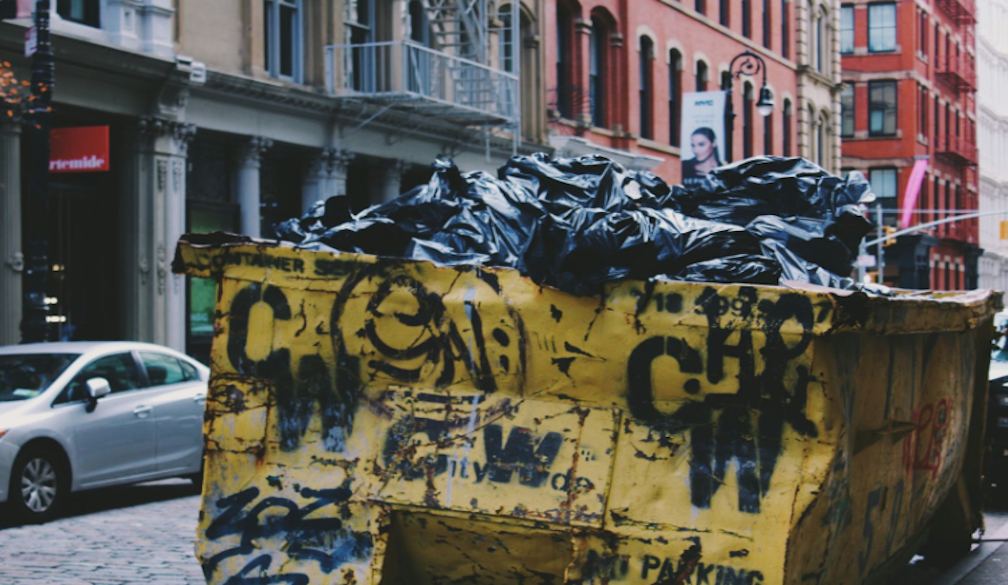
It’s imperative that companies use the right bin type based on the waste they’re disposing of, as incorrect waste disposal can cause issues such as damage or fines. These bins must also be the right size and designed in a way that makes them easy to use for employees and refuse collection staff. In this article, we’ll explain some of the different types of commercial waste bins and how they work.
Hook Lift Bins
Hook lift bins are large, stationary bins that are designed to be lifted by a hook from a crane. These bins are extremely heavy-duty, made from steel, and coated in a finish to prevent corrosion. They’re particularly useful for large-scale construction projects where various materials, including glass, plastic, soil, brick, and metal, will all need to be disposed of. The design allows for a large amount of heavy waste material to be stored properly before disposal. However, they can’t be used to store hazardous substances such as toxic chemicals or asbestos.
It's possible to find affordable hook bins available for purchase online. The dimensions and specifications will depend on the specific needs of the business, but luckily, hook bins for sale are available in multiple sizes and types. This means companies can order bins that are best suited to the job, ensuring that waste can be stored and disposed of safely.
Skips
Skips are one of the standard options for construction sites and industrial waste, providing suitable storage for all sorts of waste. These bins are designed to be lifted up by trucks with specialised hydraulic skip lifting frames. The specific design is universal, so no matter the size of the skip, it can be picked up safely.
These are typically open containers, although some skips also come with lids or other features such as doors, wheels or crane bins. These features make skips very versatile, and because they come in a range of sizes, they’re suitable for all kinds of waste removal projects. Skips are made from heavy-duty steel, making them ideal for storing all different kinds of waste materials. They’re also usually coated to prevent them from corroding when exposed to the elements outdoors.
Front Lift Bins
These bins are more mobile than the previous two, allowing businesses to store a variety of waste materials safely and securely while still able to be transported around a site. Front lift bins are typically colour-coded, making it easy for employees to know which bin is used for each waste type. This helps improve waste disposal and reduces the possibility of fines for improper disposal.
Aside from being colour-coded for easier use, these bins also come with chains and padlocks to ensure they can be used safely. When not in use, bins are locked to prevent misuse and keep the site secure.
Food Waste Bins
Food waste is a big problem for many businesses. While it can be disposed of in regular bins, it often creates a smell and can attract pests such as rats and mice. These can cause serious health risks for employees and customers, so proper disposal is essential. Food waste bins are designed to store waste food hygienically, reducing smell and preventing pest infestations.
One of the main features of a food waste bin is that the lid is fixed to the body, preventing spillage and allowing for it to be secured properly. A separate inner container and net bottom can also help to reduce the amount of moisture, eliminating bad smells.